Housings for test benches and testers by MSG Equipment: the perfection is always in the details
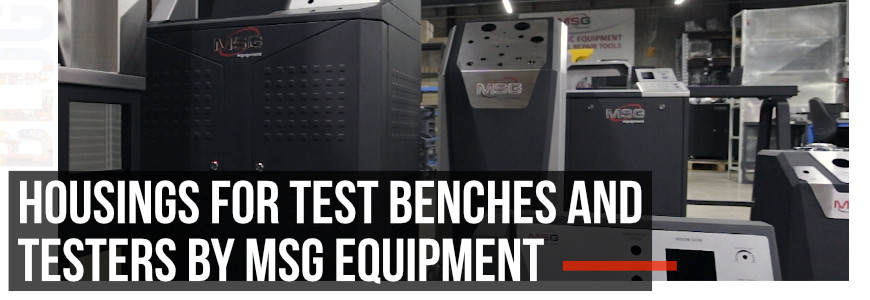
- Design
- Basic Characteristics
- Design
- Metal bending on CNC presses
- Installation of fasteners
- Anticorrosive coating
- Logo and information inscriptions
- Ergonomics
Our goal – to increase the level of automation of work processes in car services, service stations, workshops. MSG Equipment can minimise manual labour and significantly reduce service/diagnostic/repair time.
The process of development and manufacturing of enclosures for MSG Equipment stands and testers is also maximally automated. Our experts are involved in the creation of the 3D model and the assembly procedure, all other processes – automated.
All other processes are automated.
Design
At the initial stage of enclosure creation, we develop a special 3D model and design drawings of the future stand shell. We determine the overall size, design features, functionality, manufacturability and appearance of the enclosure. We carefully consider and calculate every element and detail of the enclosure.
Main features of MSG Equipment stand enclosures:
- branded style;
- high strength;
- rigidity;
- lightness;
- ergonomics;
- safety.
Design
Bodies of the stands can withstand high loads without deformation, as some units require high forces and torques for diagnostics. For example, the MS1000+ shock absorber diagnostic bench can test any type of shock absorber under a load of up to 1000 kilograms.
We use a space-tube frame construction with local reinforcement elements in the stand bodies. The main part of the frame parts of the enclosure is manufactured by laser cutting on a special CNC machine. With the help of laser we cut out individual construction elements of any configuration and size. To join the individual parts of the hull, we use carbon dioxide welding or argon welding, depending on the materials to be welded.
This produces a monolithic lightweight structure that provides the necessary strength and rigidity.
Bending of metal on CNC presses
We use CNC bending presses to bend sheet metal reamers. Using bending presses, we can easily realise the most daring design solutions, providing the necessary rigidity of the enclosure, without introducing additional elements into the construction.
Fixing hardware
In all MSG Equipment bench and tester enclosures, we have provided dedicated mounting locations for boards, cable leads, control panels, etc. Using press-fit or welded threaded elements, we mount radio and electronic components into the enclosure.
Anticorrosive coating
To protect metal enclosures from corrosion, we use paint or electroplating. We use powder coating technology to apply the paint coating. Among its main advantages are resistance to mechanical influences and the ability to be used in all climatic conditions.
In addition, this method of colouring gives our enclosures a more attractive appearance, increases electrical protection and wear resistance of the surface, as well as environmental friendliness due to the absence of solvents in the paint. Elements of the enclosures that come into contact with aggressive media, such as brake fluid, are made of stainless steel. This is the case with the MS300 brake caliper diagnostic stand.
Logo and information inscriptions
There are inscriptions on our equipment that carry important information and help the technician to work with the stands. They should be clear and easy to read at all times. For example, «Load», «Drive RPM», «Voltage». We put logo and other information on the case by UV-printing. Each stand or tester has an information plate with a unique product number and laser engraved inscriptions.
Ergonomics
The dimensions of the enclosures and the arrangement of all elements on the enclosures meet ergonomic requirements, which ensures comfortable work with our equipment. When composing the elements of the enclosures, we pay great attention to service openings, windows and doors for the most convenient maintenance of the stand during operation. This can be seen on the example of the MS1000+ shock absorber diagnostic and repair stand.
All design and technological solutions adopted in the manufacture of enclosures ensure long service life of our equipment, as well as convenience and safety during operation.